生産技術開発のミッションは、「効率的な生産」によって迅速かつ安定的な製造工程を実現するために、設備やシステム等の策定・実行を行うことです。
特に私のいる「長崎TEC」は製品であるイメージセンサーを作るFabが複数あるため、それぞれのFabの設備やシステムなどの特性、その時々の状況、FabとFabをつなぐ物理的な搬送能力など、複雑なものごとを踏まえて最適な製造工程をつくる必要があります。それを私たちの言葉では、効率の良い「もの流し」と言います。
製品が完成するまでのリードタイムを短縮することができれば、それだけ素早く製品をお客様にお届けすることができ、会社の競争力にもつながるため、最適かつ最速な「もの流し」を目指した取り組みを行っています。
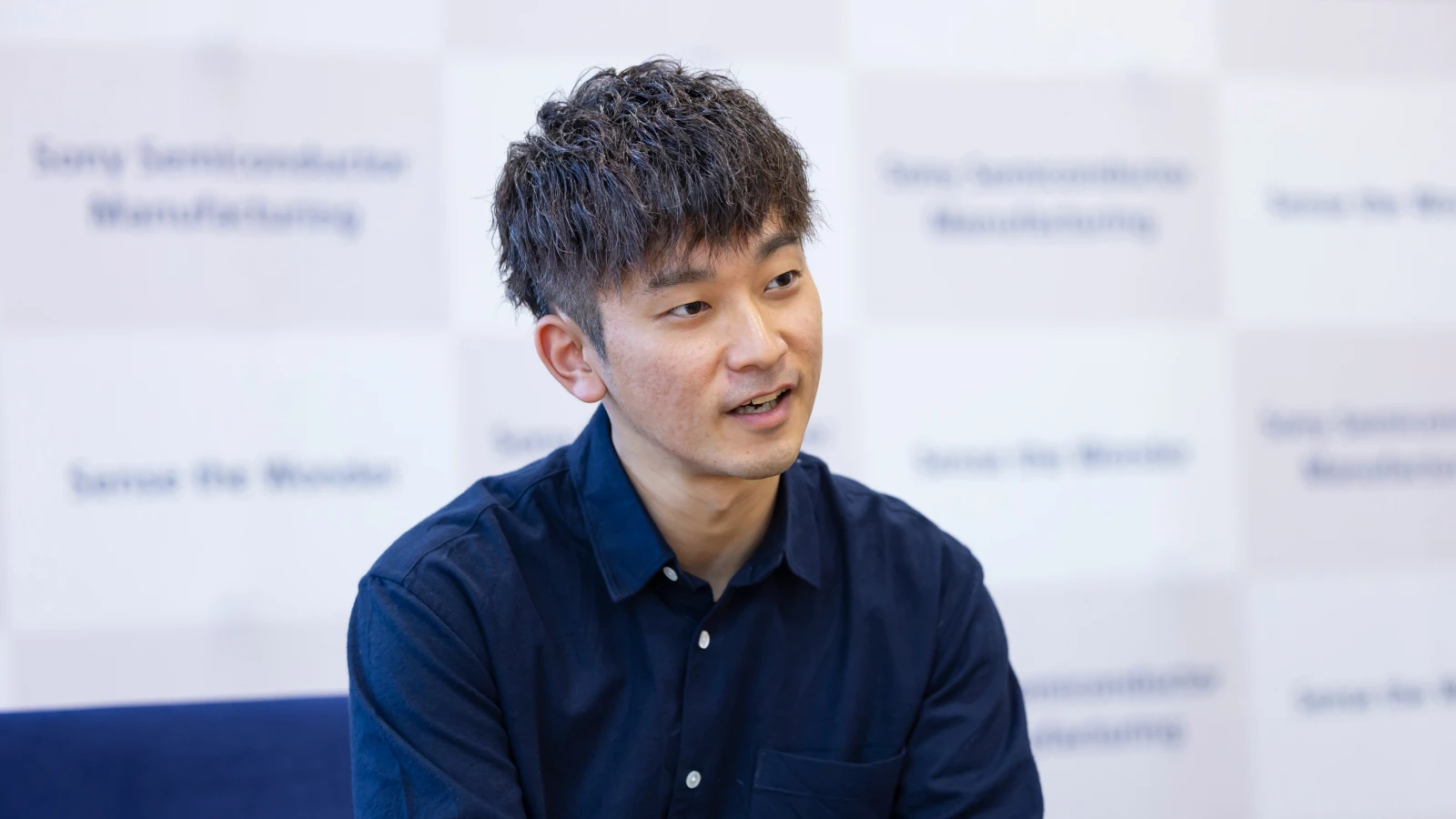
新工場立上げ時における「搬送スケジューラシステム」のリニューアルを海外メーカーと協業して構築しました。
ひとつのイメージセンサーをつくるためには、500〜600の製造工程があり、そのひとつ一つの工程ごとに最適なFabへ製品を搬送する必要があります。つまり製造にかかるリードタイムの大きな部分に搬送時間が影響しているのです。
新工場立ち上げ前に行われた調査結果では、既存の搬送スケジューラでシステムでは、製品をFabからFabへを搬送数が無駄に増えてしまい、物理的にも搬送能力の限界を超えてしまうことがわかっていました。そこで、搬送数を抑えてリードタイムを短縮しつつ、生産能力が落ちない、新しい搬送スケジューラシステムを開発することになり、私はその担当になりました。
開発パートナーに選んだのは海外のメーカーだったため、英語でコミュニケーションをしながら、システムの仕様検討や設計相談をしながらプロジェクトを進めました。
完成までに約3年を必要としましたが、無事に新しい搬送スケジューラシステムへの切り替えが終わり、現在長崎TECでは安定したもの流しが行われています。
なお、当初は課題だと思っていた英語のコミュニケーションですが、現在では自然にコミュニケーションできるようになり、現在では事前に英語の原稿を書かずに、その場で資料を見ながらミーティングを行えるようになりました。
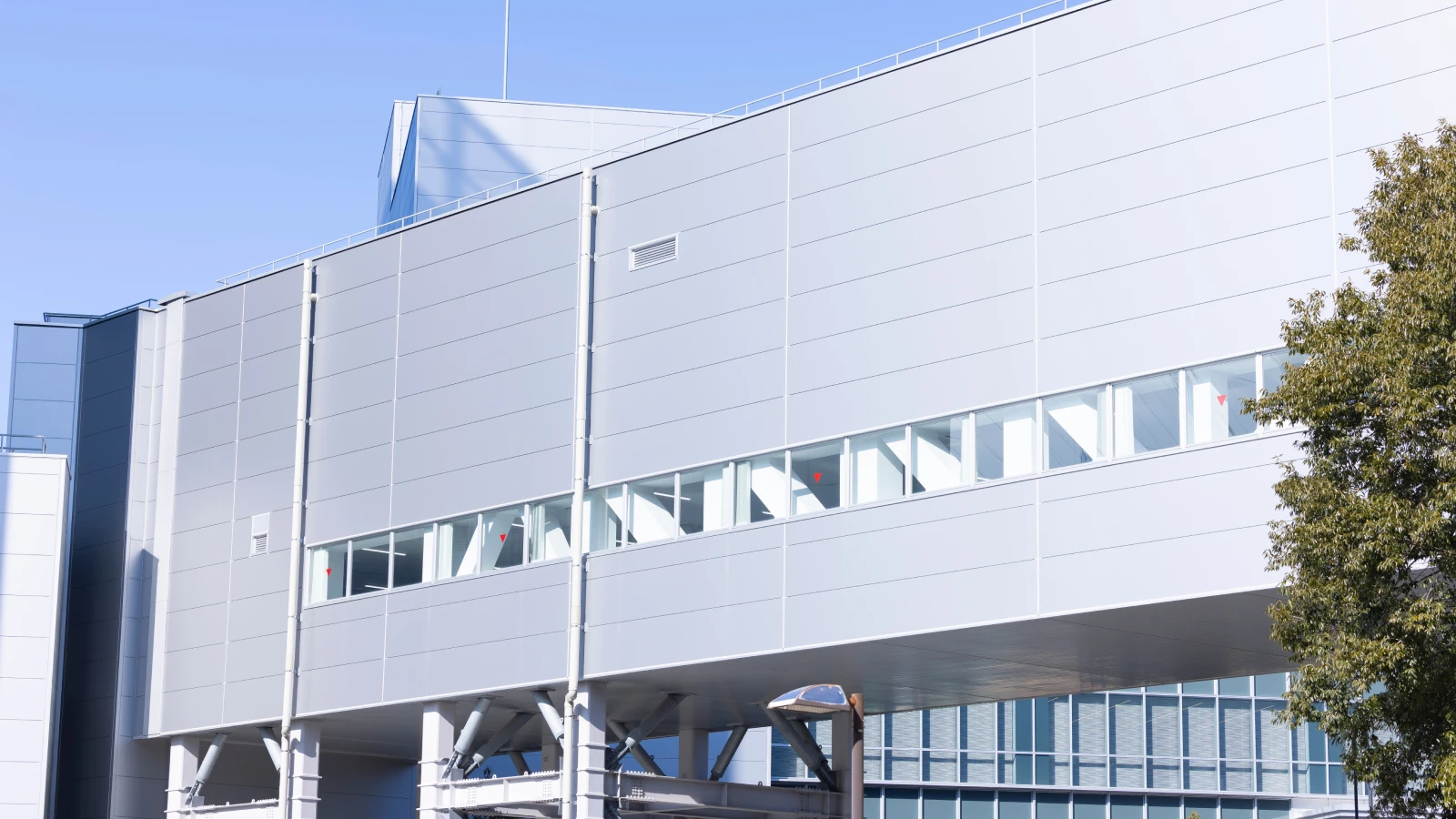
私たち生産技術開発のシステムメンバーで考えたロジックで工場全体が動いている。そう思った時に大きなやりがいを感じます。
「システム」というと、ものづくりには直接的な関係がない縁の下の力持ち、裏方なのでは?というイメージが強いかもしれませんが、実はそうではありません。なぜならシステムのインフラ基盤がなければ、効率的なものづくりは成立しないからです。
ものづくりをする工場・会社にとって、効率的な(早く安定した)ものづくりは、非常に重要であり、そんな重要な部分を私たちがロジックから考え、実際に開発をして「もの流し(工場全体の製造工程)」を革新することができる。私たちの仕事にはそういった魅力があると実感しています。
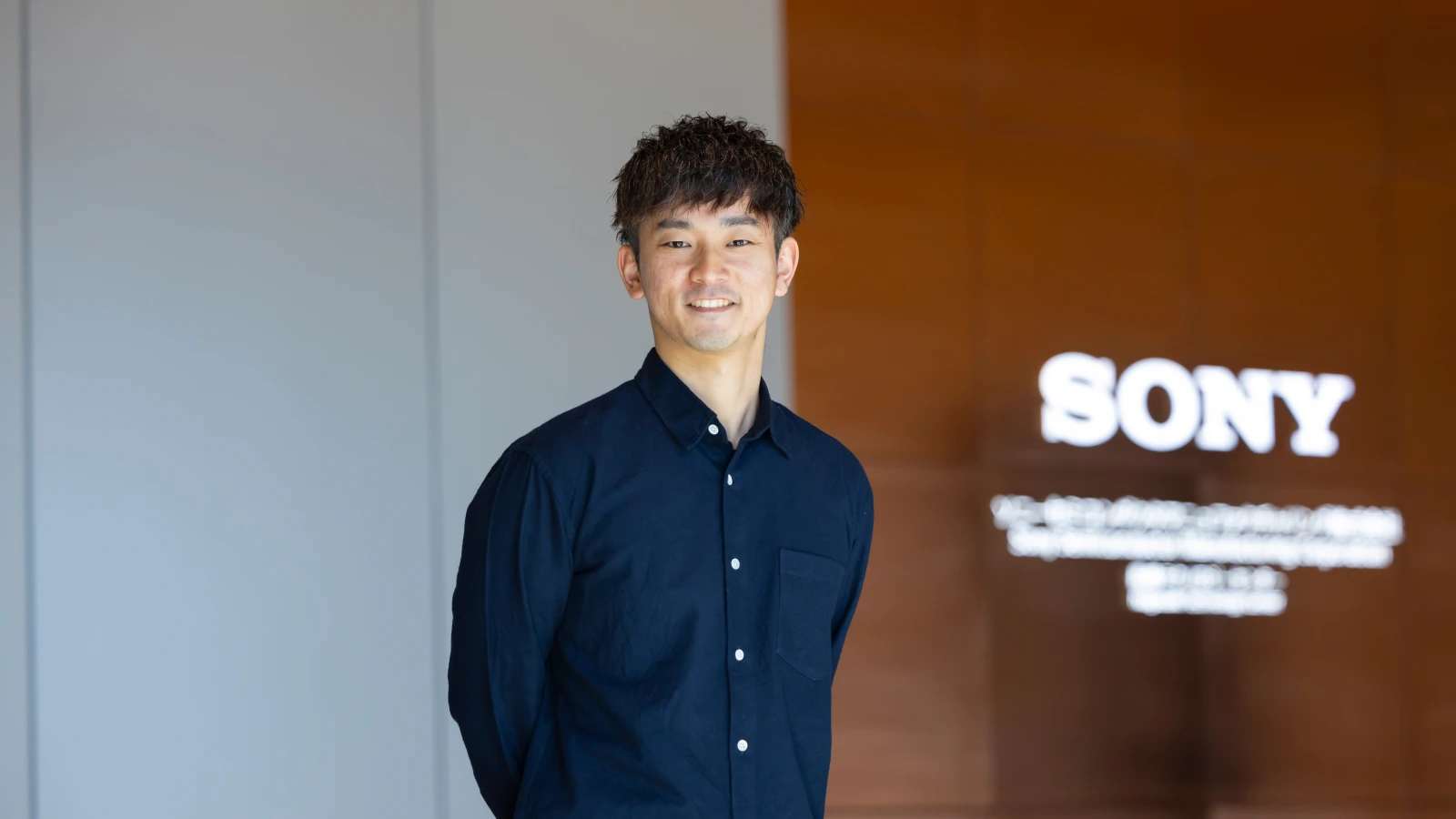